UZUPEŁNIENIE DO
CIĄGU TECHNOLOGICZNEGO PRZETWARZANIA SUBSTRATÓW
elektrociepłowni biogazowej
ADRES
| :
| działka 243/24 obręb Brzeżno, Gmina Brzeżno
Powiat Świdwin , woj. zachodniopomorskie
|
WŁAŚCICIEL
| :
| Biogazownia Brzeżno Sp. z o. o.
Brzeżno 30, 78-316 Brzeżno
|
|
|
|
OPRACOWAŁA
| :
| mgr inż. Jerzy Świergiel
|
Brzeżno styczeń 2015 r.
1.0 Charakterystyka obiektów wchodzących w skład instalacji biogazowej 3
2.0 Opis procesu technologicznego produkcji biogazu, energii elektrycznej i energii cieplnej. 5
2.1. Przygotowanie substratów. 6
2.1.1. Dozowanie substratów do komór fermentacyjnych. 6
2.3. Stan zapełnienia zbiorników.. 8
2.7. Produkcja biogazu. 11
2.8. Magazynowanie biogazu. 11
2.9. Uzdatnianie gazu. 13
2.10. Pomiar składu chemicznego gazu. 14
2.11. Wykorzystanie biogazu. 14
2.12. Wykorzystanie ciepła. 14
2.13. Wykorzystanie energii elektrycznej 14
3.0 Przeznaczenie oraz miejsce zastosowania pozostałości pofermentacyjnych. 16
4.0 Określenie położenia biogazowni i fermy trzody chlewnej. 17
1.0 Charakterystyka obiektów wchodzących w skład instalacji biogazowej
Obiekty wchodzące w skład biogazowni:
Zbiornik fermentacyjny – trzy przegrodowy
• powierzchnia zabudowy łączna - 1.698,59 m2
• objętość biomasy łączna - 8.790,43 m3
1. przegroda fermentatora I stopnia średnicy 28,80 m – „1”
• powierzchnia zabudowy - 651,44 m2
• objętość biomasy - 3384,92 m3
2. przegroda fermentatora I stopnia średnicy 24,80 m – „2”
• powierzchnia zabudowy - 483,05 m2
• objętość biomasy - 2486,88 m3
3. przegroda pofermentacyjna średnicy 26,80 m – „3”
• powierzchnia zabudowy - 564,10 m2
• objętość biomasy - 2918,63 m3
4. zbiornik wstępny na surowce płynne średnicy 7,40 m – „4”
• powierzchnia zabudowy - 47,78 m2
• objętość biomasy - 135 m3
5. pompownia „5” umieszczona pomiędzy zbiornikami fermentatorów
• powierzchnia zabudowy -111,25 m2
6. płyta separatora osadu „6”
• powierzchnia zabudowy - 35,00 m2
7. kontener kogeneracyjny „7” budynek kontenerowy
• powierzchnia zabudowy - 36,60 m2
• wysokości -3,0 m
8. budynek stacji transformatorowej „8”
• powierzchnia zabudowy - 10,20 m2
• wysokości -2,72 m
9. pochodnia gazu „9”
• powierzchnia zabudowy - 4,00 m2
10. dozownik surowca „10”
• powierzchnia zabudowy - 41,25 m2
11. drogi utwardzone, plac manewrowy „11”
• powierzchnia zabudowy - 1.827,03 m2
12. istniejące częściowo zadaszone silosy surowca „12”
• powierzchnia zabudowy - 2747 m2
13. studnia kondensu „13” - 1 szt.
14. maszty odgromowe „14” - 6 szt.
15. filtr węglowy „15”
• powierzchnia zabudowy - 4,0 m2
1.1. Zestawienie urządzeń i maszyn technologicznych.
Lp.
| Wyszczególnienie
| Opis
| Producent
|
1
| Dozowniki surowca stałego
| pojemność 30 m3 x 1 szt
| Konrad Pumpe GmbH
|
2
| Centralna pompa dozująca
| 22kW z falownikiem
| Vogelsang
|
3
| Miernik przepływu gnojowicy
| Dn 200
| Endres+Hauser
|
4
| Zawór przelewowy
| Dn 400
| Gefa
|
5
| Pompy z suchym wirnikiem
silnika, układ króćców in-line, z
elektroniczną regulacją
obrotów, Q ? 8,0m3/h
| wysokość podnoszenia
120dm, temperatura
otoczenia 40oC lub więcej,
temperatura medium 140oC
lub więcej
| Grundfos
|
6
| Mieszadła
| Wolnoobrotowe poziome
mieszadło łopatkowe
| Karl Buschmann, Agrikomp
|
7
| Dach chroniący przed
niepogodą PVC wytrzymałość
1000kN/m2
|
| Hepolan Heeren GmbH
|
8
| Osłona gazu
| EPDM folia 2,0 mm
| Hepolan Heeren GmbH
|
9
| System pomiaru zawartości
CH4
| Analizator biogazu
| AWITE
|
10
| Szafa sterująca TEWE
| Układy programowalne do
sterowania procesem
technologicznym w instalacji
|
|
11
| Silniki MWM w kogeneracji
| 1 szt. 800 kW
| SEVA Energie A.G.
|
12
| Generatory prądu zmiennego
| Generatory synchroniczne
Marelli , 800 kVA ,
| Marelli
|
13
| Czujniki temperatury PT100
| Sonda do pomiaru temp.
|
|
14
| Transformator
| Typ KSWp 2550/4000
Olejowy, 1000kVA
|
|
15
| Rozdzielnica Średniego
napięcia
| Roz. Modułowa typ SM6
produkcji Schneider
| Schneider
|
16
| Gazomierz
| Pomiar ilości gazu
|
|
17
| Czujnik stanu zapełnienia
zbiornika
| Pomiar napełnienia zbiornika
|
|
18
| Czujnik temperatury
| Termometr elektryczny, analogowy
|
|
19
| Agregat sprężarki powietrza
| Utrzymywanie membrany dachowej zbiorników
|
|
2.0 Opis procesu technologicznego produkcji biogazu, energii elektrycznej i energii cieplnej.
Substrat ciekły w postaci gnojowicy świńskiej będzie przywożony beczkowozem do zbiornika wstępnego znajdującego się na terenie biogazowni o poj. ok. 135 m3. Następnie będzie wpompowany bezpośrednio do zbiorników fermentacyjnych o łącznej pojemności ok. 5.871,80 m3. Dystrybucja gnojowicy następuje poprzez blok rozdzielczo pompowy znajdujący się w pomieszczeniu pompowni. Pozostałe substraty stałe ( kiszonka kukurydzy, kiszonka GPS, kiszonka traw, wysłodki buraczane itp.) będą dostarczane w miarę potrzeb i wsypywane do dozownika za pomocą ładowarki i dalej do wg. założeń technologicznych automatycznie dozowane do fermentatora I stopnia. Pojemność zasobnika wystarcza na 12 godzin zapotrzebowania wsadu. Od zbiorników fermentacyjnych masa będzie przepompowywana do zbiornika pofermentacyjnego o pojemności 2918,63 m3. Tutaj będzie następował w dalszym ciągu proces fermentacji wtórnej. Napełnianie zbiornika będzie odbywało się grawitacyjnie na zasadzie naczyń połączonych oraz zestaw pomp. Dystrybucja stałych substratów wsadowych z okrągłych zbiorników fermentacyjnych odbywa się poprzez system pomp znajdujący się w pomieszczeniu pompownia (pompy, zawory), które znajduje się pomiędzy zbiornikami. Wszystkie substraty są poddane procesowi fermentacji beztlenowej w szczelnym i podgrzanym do ok. 38oC Zbiornikach fermentacyjnych. Po zdefiniowanym czasie fermentacji substraty przepompowywane są dalej do zbiornika na odpady pofermentacyjne również szczelnie zamkniętego. Stąd masa pofermentacyjna będzie odbierana przez specjalistyczne maszyny do rozwozu masy ciekłej i rozlewana na pola, które są w użytkowaniu przez właściciela zakładu biogazowni i są one oddalone do 6,0 km od biogazowni. Powstały w wyniku fermentacji biogaz magazynowany jest w górnej części zbiorników, z których to jest kierowany do urządzenia zagęszczania biogazu, a później po oczyszczeniu i sprężeniu spalany w silniku prądotwórczym zlokalizowanym w kontenerze kogeneracyjnym – obiekt nr „7”. W wyniku odzysku ciepła ze spalin powstałych ze spalania gazu oraz chłodzenia silnika mamy odzysk ciepła w wymienniku, produkowana jest ciepła woda, która będzie przekazywana rurociągami do sąsiedniej obory trzody chlewnej i na potrzeby własne biogazowni. Wyprodukowana energia elektryczna zostaje dostarczana do sieci energetycznej i jest sprzedawana. Ciepło wykorzystywane jest w około 20% na potrzeby własne biogazowni (ogrzanie zbiorników fermentacyjnych) jak i może być wykorzystane do innych zewnętrznych celów technologicznych np. do produkcji pary. Reszta ciepła, o ile nie będzie zagwarantowany odbiór na nią, zostanie poprzez awaryjne chłodzenie agregatów schłodzona i oddana do otoczenia (chłodnice montowane fabrycznie na kontenerze kogeneracyjnym). Zbiorniki fermentacyjne są połączone ze sobą poprzez układ rurociągów technologicznych, przez co możliwe jest pompowanie substratu (na wypadek awarii) z jednego do drugiego zbiornika fermentacyjnego za pomocą bloku technologicznego usytuowanego
w pomieszczeniu pompowni. Fakt ten umożliwia wysoką efektywność i stabilność procesu biologicznego biogazowni.
Substraty stałe takie jak kiszonka z kukurydzy, wysłodki buraczane, kiszonka traw są przechowywane w silosach przejazdowych na terenie zakładu biogazowni, rękawach foliowych bądź pryzmach na terenach użytkowanych przez właściciela biogazowni w miejscowości Brzeżno. Substraty ciekłe takie jak gnojowica świńska będzie dostarczana z fermy w Brzeżnie zlokalizowanej
w sąsiedztwie zakładu biogazowni. Dostawa będzie odbywała się za pomocą beczkowozu w systemie Just In Time. W razie większego zapotrzebowania na gnojowicę tylko świńską będzie dostarczana z okolicznych ferm np. fermy trzody chlewnej. W przypadku zapotrzebowania na gnojowicę bydlęcą źródło dostawy uzgodnione zostanie z Powiatowym Lekarzem Weterynarii w Świdwinie. Obrót surowcami będzie się odbywał na podstawie procedur zawartych w systemie opartym na HACCP, który zostanie wdrożony w biogazowni.
2.1.1. Dozowanie substratów do komór fermentacyjnych.
Substraty stałe.
Substraty stałe będą dostarczane poprzez dozownik połączony z podnośnikiem ślimakowymi z komorą fermentacyjną I stopnia – zbiornik średnicy 28,8 m i ładowany za pomocą ładowarki teleskopowej.
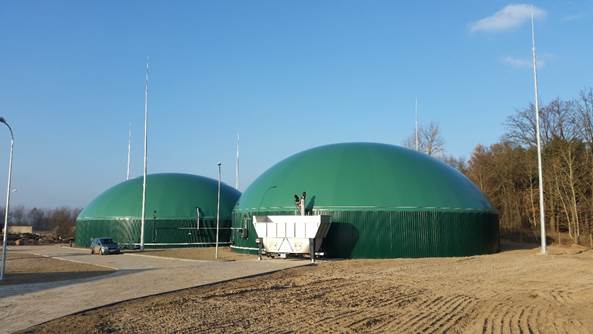
Dozownik substratów stałych.
W dozowniku są zamontowane wagi, które będą warzyły dostarczane substraty. Waga dostarczonych substratów będzie rejestrowana i archiwizowana na komputerze, na którym jest program do zarządzania technologią (PdZT). Dawkowanie ilości substratów odbywać się będzie również dzięki PdZT, gdzie będzie ustalona optymalna dawka dozowania. Podawanie substratów do zbiorników fermentacyjnych będzie odbywać się w trybie ciągłym z interwałem godzinnym przez 24 godziny na dobę przy pomocy podnośników ślimakowych.
Substraty ciekłe.
Dostarczane substraty ciekłe (gnojowica świńska) będą dostarczane do podziemnego zbiornika wstępnego o pojemności 135 m
3.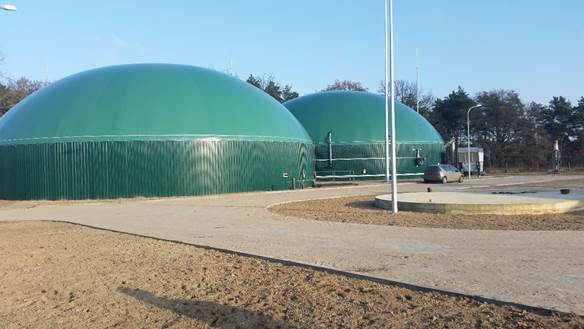
Betonowy zbiornik na substraty płynne o pojemności 135m3 (po prawej – widok płyty stropowej)
Dozowanie ilości substratów ciekłych do zbiorników fermentacyjnych będzie odbywało podobnie jak przy substratach stałych w trybie ciągłym poprzez pompę centralną i dalej dystrybuowane do zbiorników za pomocą pomp rozdzielczych. Dystrybucja będzie odbywała się w pomieszczeniu pompowni, gdzie znajduje się pompa centralna. Dzięki programowi do zarządzania technologią będzie ustalana dawka dozowania do optymalnej fermentacji. Pomiar ilości przepompowanych substratów ciekłych będzie odbywał się za pomocą przepływomierza (będzie się znajdował
w pompowi) z możliwością odczytu bezpośredniego lub w PdZT, gdzie będzie również przebiegała rejestracja danych.
Elektrociepłownia biogazowa w Brzeżnie będzie instalacją dwuetapową, pracującą według metody przepływowej, gdzie zachodzić będzie fermentacja mokra. Fermentator będzie pracować w trybie ciągłym i będzie zachodził proces fermentacji. Fermentator będzie zasilany substratem stałym przy pomocy dozownika z podajnikiem ślimakowym, natomiast substrat płynny będzie dozowany systemem rur z centralną pompą. Ze zbiornika fermentacyjnego grawitacyjnie lub za pomocą pomp masa fermentacyjna będzie przepompowywana do zbiornia pofermentacyjnego i tu będzie zachodziła fermentacja wtórna. Proces fermentacji wtórnej jest identyczny jak w zbiornikach fermentacyjnych, następuje tutaj mniejszy uzysk biogazu. Dozowanie substratów do fermentatora będzie zaprogramowana w systemie do zarządzania technologią w komputerze, który będzie się znajdował w pompowni. System również umożliwi podgląd zadanych parametrów dozowania, będzie również możliwość obserwacji ilości zadanych substratów w danym odcinku czasu, pogląd danych archiwalnych. Po fermentacji wtórnej ze zbiornika pofermentacyjnego masa będzie transportowana do zbiornika na odpad pofermentacyjny o pojemności 2918,63 m3. Zbiornik na odpad pofermentacyjny analogicznie jak pozostałe zbiorniki jest gazoszczelny i przykryty membraną.
2.3. Stan zapełnienia zbiorników
Do monitoringu stanu zapełnienia w fermentatorach i w zbiorniku magazynowym będą czujniki zainstalowane wewnątrz zbiorników. Stan zapełnienia będzie można odczytać w programie komputerowym oraz bezpośrednio sprawdzić na pomoście przez okna rewizyjne. Zbiorniki fermentacyjne w pracy ciągłej będą zapełnione na maksymalny ich poziom i przy takim stanie napełnienia będzie odbywała się fermentacja.
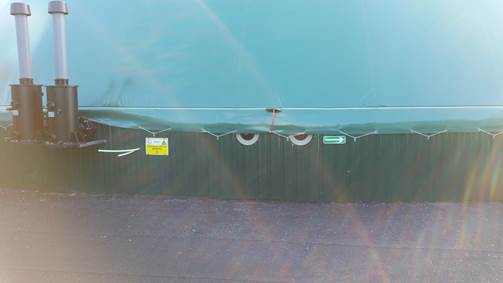
Okna rewizyjne w zbiorniku.
Większość znanych bakterii metanowych posiada optymalną temperaturę wzrostu w zakresie temperatur między 38 a 42°C. Taki przedział temperatury przewidziany jest w procesie fermentacji, ponieważ w tym zakresie temperatur osiąga się relatywnie wysoki uzysk gazu przy zachowaniu dobrej stabilności procesu. Temperatura będzie mierzona za pomocą czujników PT100 zainstalowanych
w zbiornikach (2 czujniki na zbiornik). Odczyt będzie możliwy:
- Bezpośrednio przy zbiorniku na zainstalowanym termometrze.
- W systemie komputerowym do zarządzania procesem technologicznym mieszczącym się w budynku pompowni. System ten będzie również rejestrował i archiwizował mierzoną temperaturę. Z poziomu sytemu będzie można również zadać żądaną temperaturę.
Zbiorniki będą ogrzewane za pomocą systemu rur PE za pomocą gorącej wody.
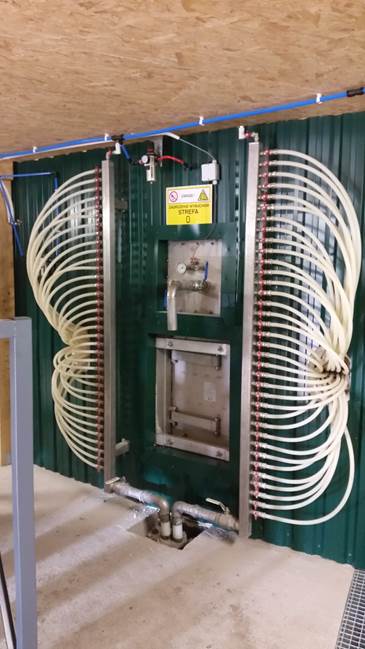
Widok zamontowanych rur PE przeznaczonych do ogrzewania zbiorników.
Przy fermentacji dwuetapowej, w przypadku bakterii produkujących kwas octowy i metan, odczyn pH musi posiadać dokładnie wartość między 6,8 a 7,5. Niezależnie od tego, czy proces przebiega jedno- lub dwuetapowo, odczyn pH ustawia się przeważnie automatycznie poprzez obecność zasadowych lub kwaśnych produktów przemiany materii, powstających podczas rozkładu beztlenowego. Pomiar pH będzie odbywał się poprzez urządzenie Titrator TIM 840 firmy HACH LANGE. Titrator jest urządzeniem przenośnym, które oprócz pH, będzie również służył do pomiaru wart. LKT/OWN, oraz potencjału redoks. Titrator będzie znajdował się w budynku biurowym na terenie gospodarstwa chlewni. Próbki do badania będą pobierane ze zbiorników poprzez „kraniki” do pobierania próbek ,które są zainstalowane w każdym zbiorniku. Pomiar będzie odbywał w odstępach siedmiodniowych (raz na tydzień). Pomiar LKT/OWN jest zaadaptowanym przez niemiecki Państwowy Instytut Badawczy ds. Rolnictwa (FAL) testem miareczkowym (metoda Nordmanna) służącym do określania ilorazu stężenia kwasów oraz pojemności buforowej w substracie fermentacji. Wartość LKT stosowana jest do oznaczania lotnych kwasów organicznych i wyrażana w jednostkach mg HAceq/l; wartość OWN to zawartość ogólna węgla nieorganicznego (alkaliczna pojemność buforowa), wyrażana w jednostkach mg CaCO3 /l. Od dłuższego czasu LKT/OWN stanowią jedne z ważniejszych wartości stosowanych do określania przebiegu procesu fermentacji. Dzięki nim w odpowiednim czasie można rozpoznać zakłócenia procesu oraz niebezpieczną utratę równowagi biologicznego rozkładu ładunku fermentacji, oraz przedsięwziąć odpowiednie środki. W przypadku pomiaru LKT/OWN za pomocą titratora TIM 840 w naczyniu do miareczkowania umieszcza się przygotowane próbki (5 ml) i dopełnia się wodą destylowaną do ok. 50 ml. Po zaopatrzeniu próbki w mieszadełko magnetyczne można ją ustawić pod elektrodą pomiarową titratora TIM i rozpocząć pomiar. Po ok. 5 minutach zakończone jest (automatyczne) miareczkowanie, dane są wyświetlane. Wartość OWN oraz wartość LKT dzięki wstępnie zaprogramowanej formule są bezpośrednio prawidłowo obliczane. Wszystkie wartości pomiarowe mogą być zapisane w pamięci titratora i/lub przesłane do drukarki lub komputera. Wszystkie dane z pomiarów będą zapisywane w arkuszu kalkulacyjnym w celu wyznaczenia trendu.
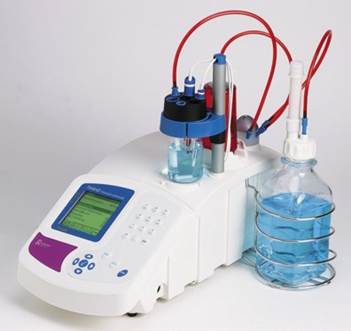
Titrator TIM 840 firmy HACH LANGE
Aby uzyskać wysoki stopień produkcji biogazu, musimy zapewnić dobry kontakt bakterii i podłoża, który ogólnie możemy uzyskać poprzez przemieszanie zawartości zbiornika z fermentowanym podłożem.
W Biogazowni Brzeżno przemieszanie mechaniczne substratu fermentacyjnego odbywać się będzie poprzez zastosowanie mieszadeł wolnobieżnych pracujących w trybie interwałowym.

Mieszadła wolnoobrotowe.
Biogaz powstaje w procesie biologicznym. Z masy organicznej przy braku obecności
tlenu oraz po spełnieniu odpowiednich warunków powstaje mieszanina gazów, tak zwany
biogaz.
Biogaz, który powstaje w wyniku fermentacji beztlenowej wytwarzany jest
w nierównomiernych ilościach i po części w okresach z wydajnością szczytową. Z tego powodu i ze względu na jak najdalej idącą stałą ilość użyteczną biogaz musi być tymczasowo magazynowany
w zbiornikach fermentacyjnych, pofermentacyjnych i na odpady pofermentacyjne. Zbiorniki magazynowe muszą być gazoszczelne, odporne na ciśnienie, media, promieniowanie UV, temperaturę i warunki pogodowe. Aby sprostać tym wymagania zbiorniki zostały wyposażone
w podwójne przykrycie membranowe (membrana dachowa, jako dach pneumatyczny, membrana gazowa). Zbiorniki pomiędzy sobą są na trwale połączone dołem stalowymi rurami i górą rurami PE HD. Zarówno ciecz jak i gaz mogą przemieszczać się grawitacyjnie. Poziom napełnienia membran biogazem realizowany jest za pomocą „ciężarka”, który wychyla się w zależności od jego ilości, oraz przez czujniki ciśnienia zainstalowane w zbiornikach. Odczyt możliwy jest bezpośrednio przy zbiornikach i w biurze w programie do sterowania technologia. Ze względów bezpieczeństwa zbiorniki magazynowe są wyposażone w zabezpieczenia przez nadciśnieniem i spadkiem ciśnienia, aby zapobiegać niedopuszczalnie wysokim zmianom ciśnienia wewnętrznego w zbiorniku. Do pomiaru ilości gazu będzie gazomierz w rurociągu gazowym. Zmierzone ilości biogazu będzie rejestrowana programie do zarządzania technologia zainstalowany na komputerze mieszczącym się
w budynku pompowni.
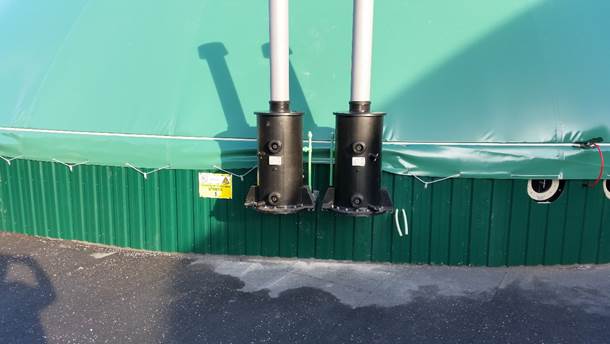
Zabezpieczenie ciśnieniowe zbiornika
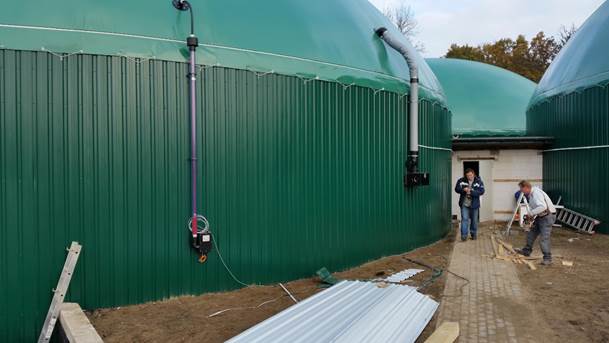
Ciężarek odchylający do pomiaru ilości biogazu w zbiorniku
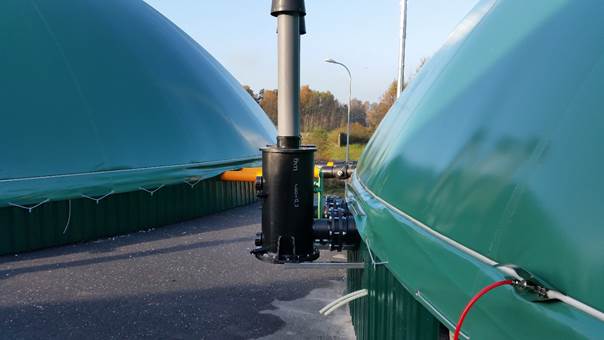
Membrany dachowe do magazynowania gazu.
Wykorzystanie biogazu odbywać się będzie w silniku spalinowym
napędzającym generator prądotwórczy. Biogaz nasycony jest parą wodną i obok metanu (CH4) oraz dwutlenku węgla (CO2) zawiera m.in. także śladowe ilości siarkowodoru (H2S). Siarkowodór jest toksyczny i ma nieprzyjemny zapach zepsutych jaj. Poprzez połączenie siarkowodoru oraz zawartej w biogazie pary wodnej dochodzi do powstawania kwasu siarkowego. Kwasy działają negatywnie na stosowane do obróbki biogazu silniki jak i dołączone do nich elementy (instalacja gazownicza, instalacja odprowadzająca spaliny itd.). Z tego powodu w instalacji przeprowadzany jest proces odsiarczania i suszenia uzyskiwanego biogazu.
Będzie przebiegało dwuetapowo:
1. Odsiarczanie biologiczne, które przeprowadzane jest w fermentatorze. W celu przeprowadzenia odsiarczania biologicznego konieczna jest obecność tlenu oraz bakterii Sulfobacter oxydans. Bakteria ta w obecności tlenu zamienia siarkowodór w proste związki siarki. W tym celu potrzebuje substancji odżywczych, które w wystarczającej ilości znajdują się w fermentatorze. Bakterie te są wszechobecne, dlatego nie istnieje konieczność oddzielnego ich dodawania. Potrzebny tlen doprowadzany jest do fermentatora poprzez wdmuchiwanie powietrza przy pomocy niewielkiego kompresora.
2. Odsiarczanie w filtrze węgla aktywnego, zlokalizowanego na bloku betonowym obok kontenera kogeneratora.
Suszenie
Aby chronić agregaty służące do wykorzystania gazu przed wysokim zużyciem, należy
z biogazu usunąć parę wodną. Ilość wody wzgl. pary wodnej, jaką może przyjąć biogaz zależna jest od temperatury gazu. Względna wilgotność biogazu wynosi w fermentatorze 100%, tym samym biogaz jest nasycony parą wodną. Przez chłodzenie gazu część pary wodnej oddziela się w formie kondensatu. Chłodzenie biogazu w biogazowni przeprowadzane będzie w instalacji gazowej. Poprzez odpowiedniego kąta nachylenia instalacji gazowej, kondensat zbierany będzie we wbudowanym zbiorniku w najniższym punkcie instalacji. Instalacja poprowadzona jest podziemnie, dzięki czemu lepszy jest efekt chłodzenia. Warunkiem należytego chłodzenia biogazu w instalacji gazowej jest wystarczająca do chłodzenia długość tej instalacji. Oprócz pary wodnej z biogazu poprzez kondensat usuwana jest także część innych, niepożądanych składników, jak rozpuszczalne w wodzie gazy i aerozole. Zbiornik na kondensat będzie regularnie opróżniany i dlatego będzie do niego zapewniony dobry dostęp. Montaż zbiornika kondensatu będzie zapobiegać zamarzaniu zbiornika.
2.10. Pomiar składu chemicznego gazu.
Będzie odbywał się za pomocą analizatora gazu, który będzie wpięty w instalację gazową w pomieszczeniu siłowni. Wszystkie dane z analizatora będą dostępne na komputerze z
zainstalowanym systemem do nadzorowania biogazownią. Dane te można również odczytać bezpośrednio na urządzeniu. Analizator będzie mierzył:
- zawartość tlenu w biogazie
- zawartość metanu w biogazie
- zawartość dwutlenku węgla w biogazie
- zawartość tlenku węgla
- zawartość siarkowodoru
a) biogaz może zostać bezpośrednio spalony, bez dodatkowej obróbki
b) w opisywanym rozwiązaniu biogaz spalany będzie w elektrowni kogeneracyjnej
Elektrociepłownia kogeneracyjna pracuje według zasad równoczesnego wytwarzania energii elektrycznej i ciepła w jednym procesie termodynamicznym. Agregat w wyniku spalania biogazu będzie wytwarzał energie elektryczną w skojarzeniu z ciepłem. Zastosowany jest silnik spalinowy o zapłonie iskrowym, 8 - cylindrowy, napędzany biogazem. Na wspólnym wale zespołu znajduje się generator synchroniczny z wzbudnicą zamieniający energię spalania w energię elektryczną. Dodatkowo z układu chłodzenia bloku oraz ze spalin poprzez wymienniki pozyskiwana jest przy tym energia cieplna.
2.12. Wykorzystanie ciepła
Pozyskiwane ciepło z silników kogeneracyjnych będzie miało sprawność termiczną ok. 40,0%. Poprzez wymienniki zamontowane na silnikach ko generacyjnych będzie dystrybuowane przez pompy i rozdzielacz i doprowadzane do rożnych odbiorników w tym między innymi w około 20% wykorzystane na potrzeby własne do procesu technologicznego na ogrzewanie zbiorników. Ciepło również zostanie dostarczone do sąsiedniej chlewni trzody w Brzeżnie na potrzeby CO i CWU. Reszta ciepła, o ile nie będzie zagwarantowany odbiór na nią, zostanie poprzez awaryjne chłodzenie agregatów schłodzona i oddana do otoczenia (chłodnice montowane fabrycznie przy silnikach kogeneracyjnych).
2.13. Wykorzystanie energii elektrycznej
Do wytwarzania energii elektrycznej i ciepła zostanie wykorzystany agregat BHKW (kogeneracyjny) o mocy elektrycznej do 800 kW. Urządzenie ma zapotrzebowanie na biogaz ok. 330 m3/h +-5% i przy zawartości metanu ok.60%, wytwarza moc pierwotną w ilości 6,0 kWh/m3. Posiada sprawność elektryczną ok. 42,0%, sprawność termiczną ok. 40,0 %. Agregat będzie znajdować się w kontenerze. Będzie on posiadał odrębny system nadzorowania, do którego będzie miał zdalny dostęp producent kogeneratora.
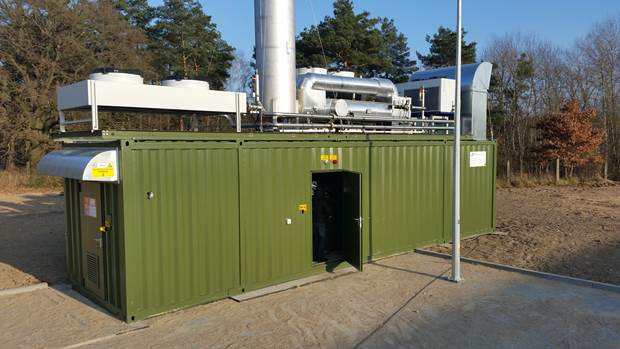
Kontener kogeneratora
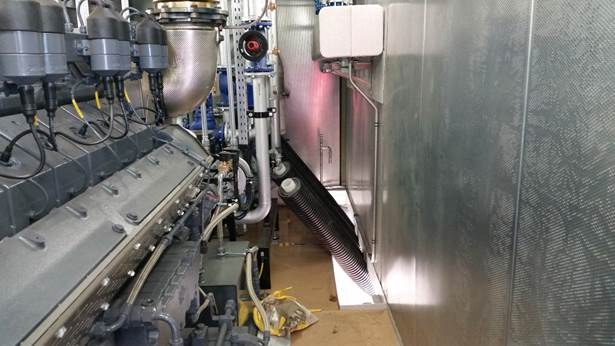
Agregat prądotwórczy do wytwarzania energii elektrycznej i cieplnej w skojarzeniu.
2.13.1.1. Miejsce przyłączenia i odprowadzenia energii elektrycznej.
Elektrownia biogazowa przyłączona jest do prefabrykowanej betonowej stacji transformatorowej znajdującej się na terenie zakładu biogazowni, która to wyposażona jest
w urządzenia rozdzielcze 15kV, 0,4kV oraz transformator 15/0,4kV i mocy 1,0MVA. Przyłącze wykonane jest linią 3 x XRUHAKXS 1x120/50mm2 o długości 110 m.
W przypadku nadprodukcji gazu (więcej niz. może przerobić elektrociepłownia) i podczas prac konserwacyjnych biogaz będzie spalany w pochodni gazu. Dzięki temu uniknie się emisji zapachów i metanu. Pochodnia może przerobić godzinową produkcję gazu powiększoną o 10%.
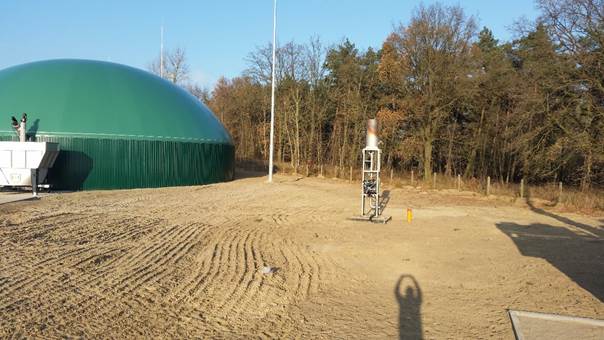
Pochodnia do spalania gazu
3.0 Przeznaczenie oraz miejsce zastosowania pozostałości pofermentacyjnych.
Materiał pofermentacyjny będzie w formie ciekłej o suchej masie od 3% do 5% . Ilość dobowa około 30 m3. Ze względu na obowiązujące przepisy gospodarka odpadami i nawożeniem pól, przewidziane jest zmagazynowanie masy pofermentacyjnej w zbiorniku pofermentacyjnym okresie zimowym na czas do 110 dni. Potrzebna kubatura zbiornika końcowego 2900 m3
W wyniku beztlenowej obróbki powstaje wysokowartościowy nawóz:
• zawarty w substratach azot w 90% przekształca się do formy amonowej.
· azot amonowy jest szybciej przyswajany dla roślin i jest trudniej wymywany z gleby niż azot azotanowy dzięki temu zmniejsza się ryzyko zanieczyszczenia azotanami źródeł wody pitnej i eutrofizacji wód powierzchniowych oraz można zaoszczędzić duże ilości nawozów
mineralnych.
· substancja organiczna jest w przeważającej części rozłożona tak, ze w powietrzu glebowym powstaje więcej tlenu dostępnego systemom korzeniowym roślin. W ten sposób mogą one lepiej pobierać z gleby azot i inne substancje pokarmowe.
· kwasy organiczne ulęgają w biogazowni rozkładowi tak, ze zarówno rośliny jak i organizmy glebowe nie będą ulegały sparzaniu.
• nasiona chwastów, jaja pasożytów i bakterie chorobotwórcze dezaktywowane są
w biogazowni w stopniu uniemożliwiającym ich dalszą aktywność. W ten sposób minimalizuje się stosowanie pestycydów i medykamentów.
· redukcja odorów z poszczególnych substratów o intensywnym zapachu o ok. 80 - 90%
w stosunku do surowej gnojowicy.
• redukcja niekorzystnych gazów cieplarnianych.
Materiał pofermentacyjny będzie w całości zużyty na gruntach należących do Inwestora biogazowni w okolicy do 10 km od biogazowni cztery razy w roku. Będzie odbierany beczkowozami, bezpośrednio ze zbiorników na odpad pofermentacyjny, które posiadają specjalne złącze z zasuwą do podłączenia węża. Za pośrednictwem grawitacji i pompy poferment będzie wpompowywany do beczkowozu, następnie wywożony i aplikowany do gruntu. Przed każdą kampanią wywozową proferment będzie badany na zawartość azotu i innych pierwiastków odżywczych i ewentualną obecność bakterii. Należy przeprowadzić badanie na obecność: beta-glukuronidazy-dodatnich, Escherichia coli, salmonelli.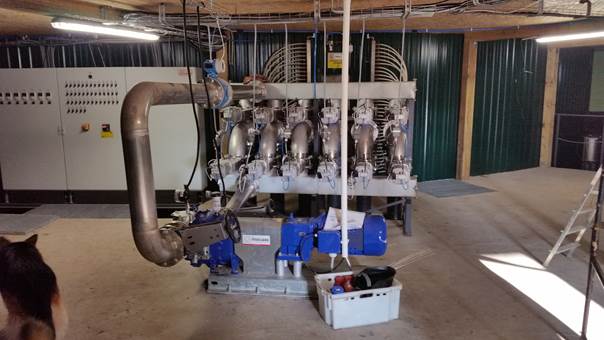
Pompa centralna w budynku pompowni
4.0 Określenie położenia biogazowni i fermy trzody chlewnej.
Biogazownia zlokalizowana jest na działce nr 243/24 w obręb Brzeżno gmina Brzeżno, powiat Świdwin woj. zachodniopomorskie. Ferma trzody chlewnej zlokalizowana jest na działce nr 243/25
w obręb Brzeżno gmina Brzeżno, i jest w bezpośrednim sąsiedztwie z biogazownią. Teren zakładu biogazowni będzie ogrodzony. Na teren zakładu biogazowni będzie można wjechać tylko przez jedną bramę od drogi dojazdowej. Biogazownia stanowić będzie obiekt zamknięty. Najbliższa odległość zabudowy biogazowni do budynku chlewni wynosi około 36 m.